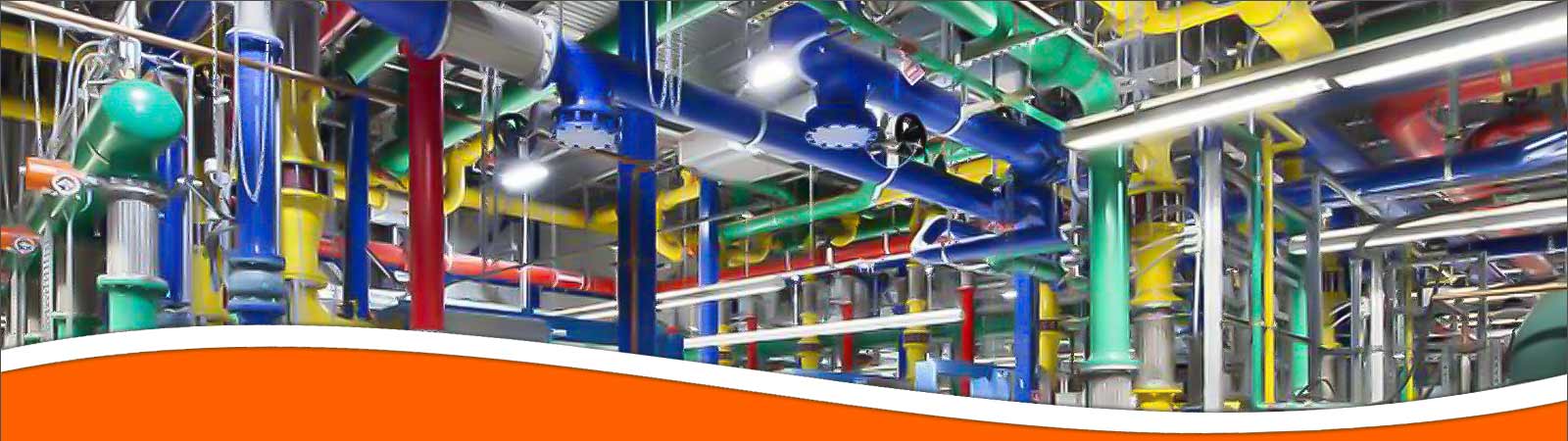
Ice, Ice, Baby: A Florida College Cools Off With TES
Florida Gulf Coast University is making headlines with a remarkable thermal energy storage (TES) system that cools campus buildings while saving the institution an average of $11,000 each month. That Savings Adds up to over $130,000 per year and is earning praise from the Florida taxpayers, who ultimately foot the bill for the University’s energy bills.
Opened in August 1997, FGCU received accreditation in less than two years—acknowledged to be the fastest record with the Colleges Commision. The 760-acre campus just east of Ft. Myers was designed to incorperate substantial green space (430 acres), in accordance with the university’s goal of being a “good house-keeper of the environment.”
Chilling Out
TES was part of Florida Gulf Coast University’s (FGCU) plans from its inception. “As the newest university in the nation, we had an opportunity to build an environmentally sound, technologically advanced campus from the ground up,” says C.R. Lyons, director of physical plant, FGCU.
Tilden Lobnitz Cooper, Orlando, the engineering firm for the facility, was the first to suggestTES. Involved in the project since its earliest planning stages, Florida Power & Light (FPL), account manager Bill Carlyle familiarized the firm with his company’s extensive demand-side management incentives for TES.
FPL allocated $7,500 toward feasibility studies, which showed that TES would offer considerable saving to the university. Once the system was installed, FGCU recieved $30 per ton ($36,000) toward system commisioning and $360,000 for the 1,200 tons of cooling shifted away from FPL’s summer peak period ($300 per ton). “With FPL’s incentives, TES turned out to be a very workable alternative for the university.” Carlyle says. The added bonus of a $186,000 cash rebate helped defray the system’s initial front-end costs.
While TES systems generally cost the same as conventional cooling systems, adding ice storage created an additional exspanse that was not anticipated in the original budget. “We had to find extra dollars over our initial innumbers to include it- but the return on investment made that easily justifiable,” Lyons explains. The lifecycle cost analysis showed the payback for a 3,600-ton-hour plant was less than five years. An added bonus is flexibility: the ice can be used as a backup source of cooling in the event of a chiller failure.
On the rocks
The engineering firm designed a two-mile chilled water loop and a complete energy management system that schedules chilled water supply according to each facility’s cooling needs. It also metered some buildings together to obtain the best electrical rates. The firm designed the central energy plant, TES system, and piping so they can be easily expanded.
In the initial phase, a 300-ton base load chiller (which operated around the clock) and a 600-ton ice-making chiller (which ran only at night) served eight buildings. As the campus grew, the expandable system allowed Lyons to add another 1,200-ton centrifugal chiller and 36 additional Calmac Ice Bank tanks, raising the cooling capacity to 406,000 sq.ft. The tanks are compact and modular with no moving parts or corrodible materials and are sited outdoors, above ground, at the campus’ central energy plant. In total, the university has 61 tanks that shifted 976 kW of electricity off-peak. Each tank has the capacity for 140 ton-hours of cooling while using 0 kW of electricity.
How it works
The Ice Bank system used at the university is comprised of a modular, insulated polyethylene tank that contains a spiral plastic heat-exchanging tube which is surrounded by water. At night, during the ice-building mode, water containing 25 percent ethylene glycol is cooled by a chiller and is circulated through the heat exchanger. The heat is extracted until eventually 95 percent of the water is frozen solid. During the night and at a temperature at 25F, the water/glycol solution circulates through the chiller and the ice tank heat exchanger. Since the solution is below freezing, water surrounding the ice tank heat exchanger is frozen. The next day the ice cools the solution from 52F to 34F during ice burn mode. The central plant piping system is arranged to let enough 52F through to mix with the 34F fluid, resulting in the desired 44F. Then the 44F fluid enteres the coil where it typically cools air from 75 to 55F. The 55F air is distributed to a high induction rate diffuser or a fan-powered mixing box where it is then fully mixed with room air to obtain the desired comfort level.
TES is a simple, enviromentally frendily process in which ice is created and stored at night when power is plentiful, inexpensive, and efficiently generated. During the day, that ice is used to cool the fluid that is circulated to a facility’s air conditioning system, thus eliminating the need to run the chiller during daytime, peak demand hours. The TES system has proven so energy efficient that the 180,000-sq.ft. Centrex building in Dallas, Texas was awarded a 99 rating- out of a possible 100- by the EPA’s Energy Star program in 2000, the first building in the US.S. to achaive such a high rating, thus making it the most energy efficient building in America, according to EPA/DOE standards.
For more information on TES, visit Calmac Manufacturing website at www.calmac.com
Back to Case Studies